
Bosch Wrocław: research and developmentīosch's R&D Center, which currently employs over 70 engineers, has been supporting both the production plant in Mirków and other factories of the Bosch concern from the very beginning, developing the company's automotive offer. Piotr Pyzio, member of the management board of Robert Bosch sp.z o.o. Thanks to the commitment and skills of our team, we have created a leading production and development center for brake system components offered by Bosch near Wrocław. Our strength lies in the creativity and high competence of our staff in every area. Over the past 25 years, our factory employees have repeatedly developed operating standards that were later implemented in other Bosch production plants. The company's representatives emphasize that the factory's success would not be possible without a strong team of employees. Currently, different types of brake systems are produced in Mirków every 3 seconds. Over the last 25 years, more than 37 million components have been produced on production lines and delivered to 5 continents. For over 33 thousand sq m area, a team of over 900 specialists develops and produces components for braking systems, which are used in vehicles of many automotive companies. Today it is a comprehensive production and research center. The Bosch brake systems plant in Mirków near Wrocław was established in 1996. Bosch Mirków near Wrocław: work and employment Rafał Rudziński, president of Robert Bosch in Poland. Today, the factory near Wrocław is responsible for the production of the most innovative elements of brake systems offered by Bosch. For 25 years we have managed to build a strong position in the concern.
#Brake pedal for bosch ibooster drivers
The concern announced the latest investment plans on the occasion of the 25th anniversary of the plant's operation in the Wrocław agglomeration.Ĭomponents manufactured at the Bosch plant in Mirków ensure the safety of millions of drivers and passengers around the world. The company is also developing a competence center to support Bosch's global business operations. New, automated production lines will be launched, on which, among others, innovative elements for electric and hybrid cars.
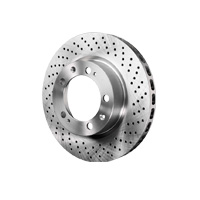
It's too bad because the MC is the same size and has the ports on the left instead of the right. That delorean thread is exactly what I stumbled upon, and oudevolvo on that forum is Lars :)ok, that's good to know, i was wondering if they were the same or not - they look similar enough, but it's hard to tell from pictures.

As long as the master cylinder is rebuildable and you can get it apart, that's the kind of thing you can do with a drill press.
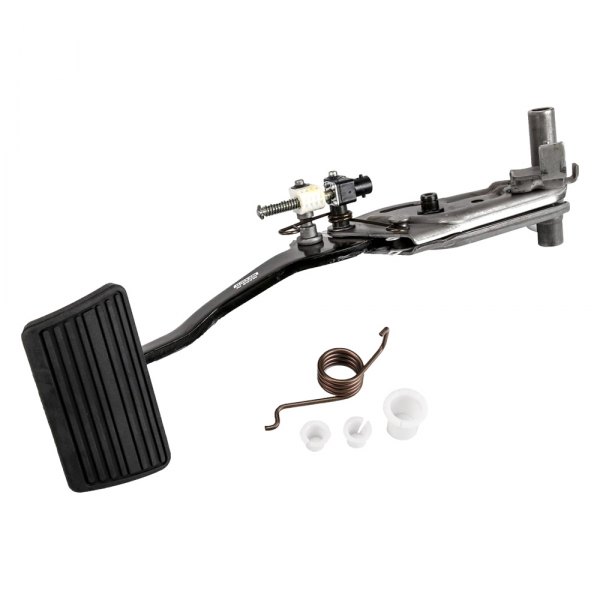
RHD masters are of course very scarce, but to avoid the seat problem and to avoid having adapters stickout out of adapters on the side of the master, facing, drilling, and tapping could make the unfinished side of the master suitable for a banjo bolt. Regarding the amount of work to tap for lines on the left. I think it would be useful to have a "silhouette" drawn of the two firewall bolts and the outline of the booster (to scale) so people can print it out to mock up. I will happily take measurements from anywhere to anywhere. We're definitely playing catch-up to him here.
